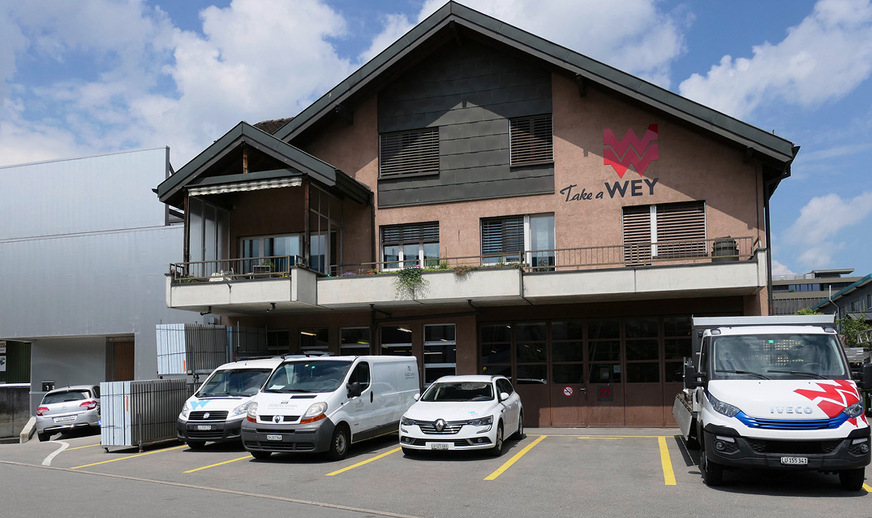
Bild: BAUMETALL
Wer der Josef Wey AG einen Besuch abstatten möchte, findet sich vor einem klassisch wirkenden Wohn- und Geschäftshaus in einer ruhigen Nebenstraße in der Schweizer Gemeinde Rothenburg wieder. Der Gebäudeaufbau ist ein vertrauter Anblick: Im Erdgeschoss befindet sich ein großes Tor, welches zur Werkstatt führt, davor gibt es vier Stellplätze für Firmenfahrzeuge, die oberen zwei Etagen könnten als Wohn- und Geschäftsräume dienen. An der Fassade ist das Firmenlogo des Unternehmens angebracht. So weit, so vertraut. Doch der Schein trügt, denn dieses Betriebsgelände verbirgt mehr in seinem Inneren, als es auf den ersten Blick möglich erscheint …
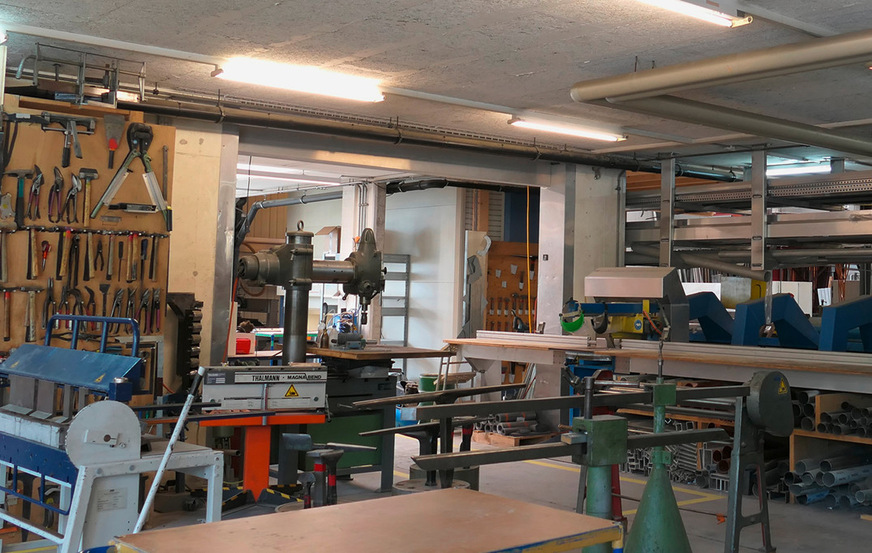
Bild: BAUMETALL
Doch zunächst verfolgt der Besucher den gewohnten Weg weiter und durchschreitet das braune Tor im Erdgeschoss. Auch hier wartet ein vertrauter Anblick, eine wunderbar bestückte und gut aufgeräumte kleine Spenglerwerkstatt, wie sie im Lehrbuch steht. Neben einer Segmentabkantbank und einer manuellen Tafelschere hängt allerlei typisches Spenglerhandwerkzeug ordentlich verstaut an den Wänden. Einzig das leichte Rumpeln und Surren von weitaus größeren Maschinen möchte überhaupt nicht zu diesem Bild passen. „Hier hat mit meinem Vater alles angefangen“, berichtet der Geschäftsführer Josef Wey mit einem leichten Schmunzeln. „Als der Platz nicht mehr reichte, sind wir mit dem Hallenanbau langsam in die Grundstückstiefe gewachsen.“
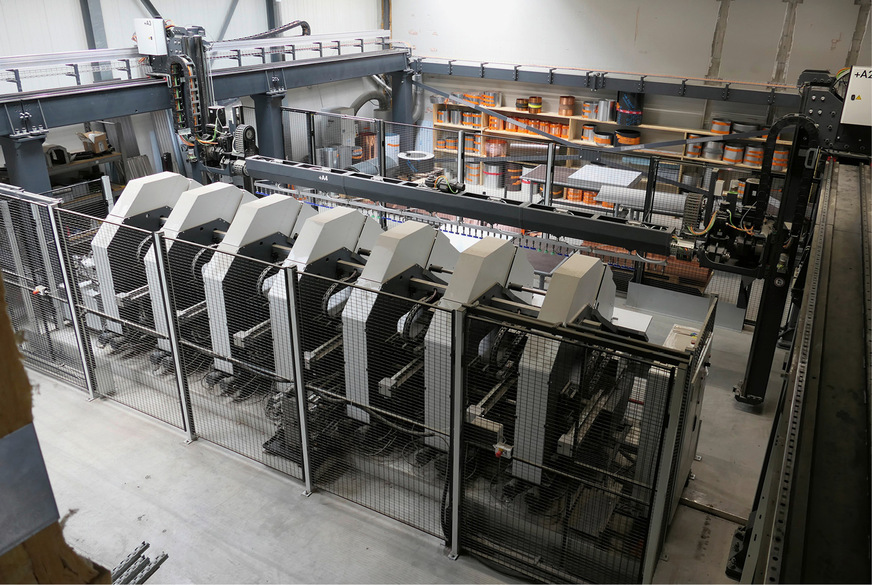
Bild: BAUMETALL
Beim Überschreiten der Grenze von Altbau zu Anbau scheint man auch eine Zeitreise durch den Maschinenbestand zu vollführen. Der Weg führt vorbei an einer Revolverstanzmaschine Trumpf Trumatic 235, Baujahr 1984, und einer Presse des italienischen Herstellers Amada, windet sich dann geschickt an einer NC-Schwenkbiegemaschine Schröder MAK 4 entlang und endet in einer hochmodernen Spenglerwerkstatt.
Zukunftswerkstatt gefunden
Die Josef Wey AG bietet Leistungen für die gesamte Gebäudehülle an. Ein Schwerpunkt des 40 Mann starken Unternehmens liegt in der Projektplanung und Ausführung von individuell geplanten Metallfassaden. Dadurch ergeben sich erhöhte Anforderungen an die Maschinen in der Fertigung. „Wir fertigen unsere Fassaden ab der Unterkonstruktion selbst. Damit verlassen wir auch den Feinblechbereich bis 3 mm und bewegen uns in größeren Materialstärken“, erklärt Josef Wey. Seit Kurzem setzt er deswegen auch auf eine Schröder Powerbend Industrial. Mit dem Up-and-down-System können Blechdicken bis 5 mm verarbeitet werden.
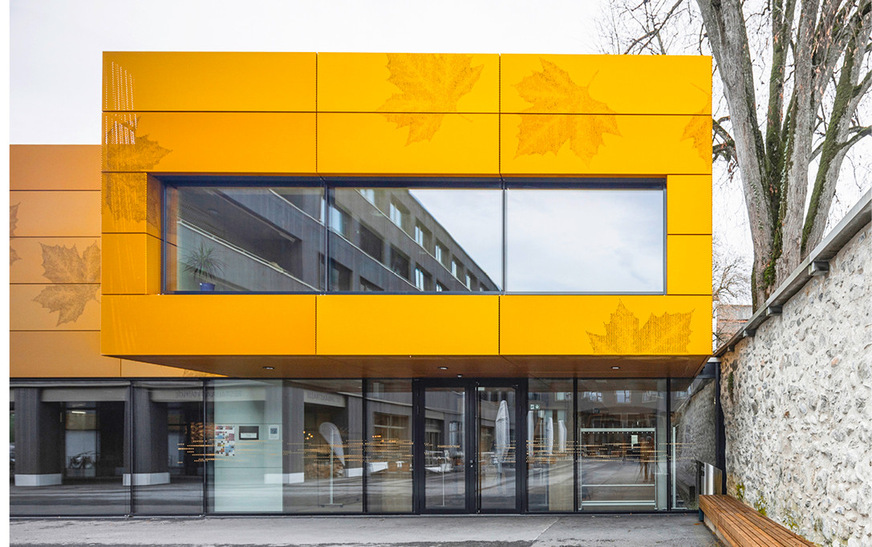
Bild: Josef Wey AG
„Durch den Schwerpunkt der Fassaden kommt es bei uns zu einer seriellen Fertigung von wiederkehrenden Elementen. In diesem Bereich wollten wir schneller werden, um weniger Kräfte in der Produktion zu binden“, führt der Metallexperte aus. So kommt es, dass Wey und sein Team anfangen, über automatisierte Fertigungslösungen nachzudenken. Als ein grobes Konzept steht, wendet sich der Unternehmer an den bekannten Langabkantmaschinenhersteller Jorns. Was folgt, ist Pionierarbeit. Das Endprodukt ist der erste Profilmanipulator JHS.
Der Erste seiner Art
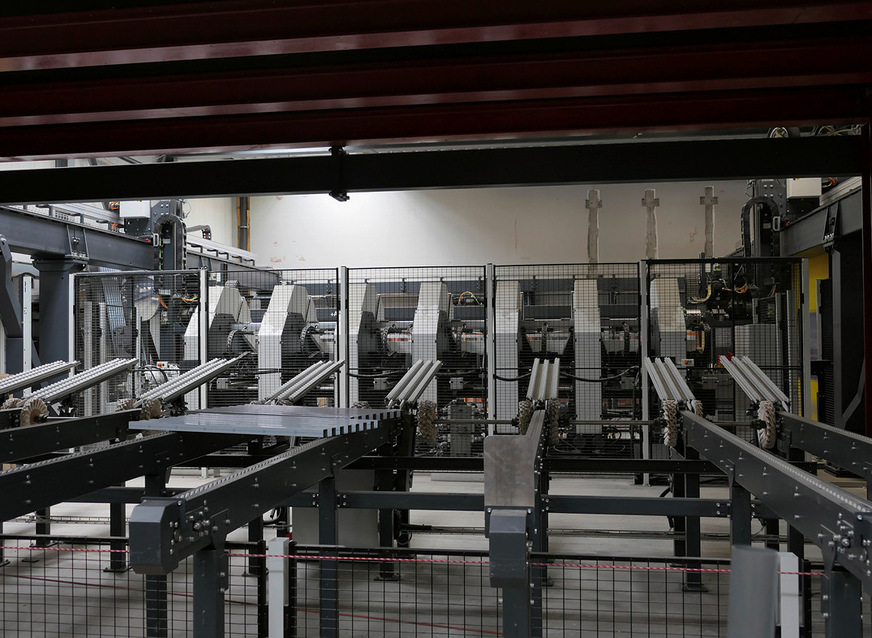
Bild: BAUMETALL

Bild: BAUMETALL
Im Zentrum der Anlage steht ein Jorns-Doppelbieger Twin Matic Pro 300. Beladen wird die Anlage über ein robotergesteuertes Handlingsystem. Mithilfe von Vakuumsaugeinheiten werden die glatten Metallzuschnitte aufgenommen und in den Doppelbieger eingelegt. Was ganz einfach klingt, hat in der Entwicklung für einiges Kopfzerbrechen gesorgt. „Das Problem bei der Aufnahme von glatten Blechen ist, dass die Saugeinheit nur einen einzelnen Zuschnitt aufnehmen soll. Wer mit Metall arbeitet, weiß, dass die Tafeln häufig aneinander haften. Wie sollte das also realisiert werden? Zunächst haben wir über Sensoren nachgedacht. Die Idee wurde aber relativ schnell wieder verworfen. Also experimentierten wir mit den einzelnen Saugköpfen und testeten unterschiedliche Kopfstärken und Höhen aus. Die Lösung für die Materialvereinzelung stellte am Schluss eine leichte Wellenbewegung dar. So lassen sich die Zuschnitte voneinander separieren“, erklärt Spenglermeister Henry Zyrus. Der Werkstatt- und Produktionsleiter der Wey AG war von Anfang an ins Projekt involviert und ist für die Steuerung des komplexen Systems verantwortlich – eine anspruchsvolle Aufgabe.
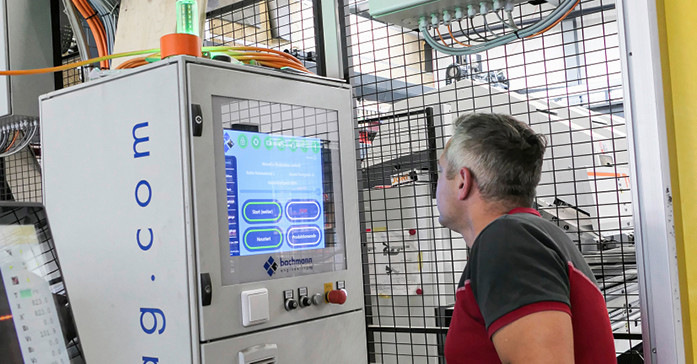
Bild: BAUMETALL
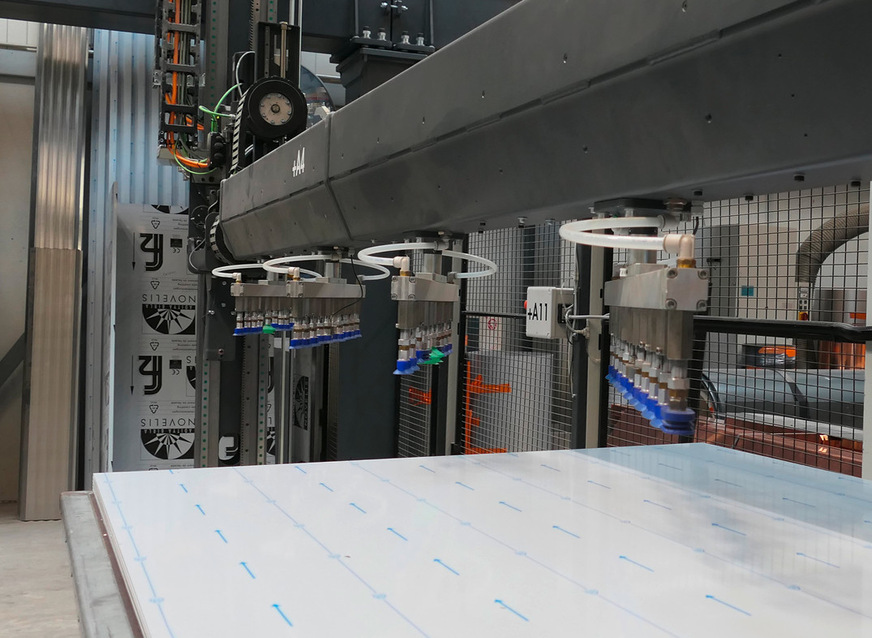
Bild: BAUMETALL
„Die Robotersteuerung des Handlingsystems ist sehr komplex, da durch die Parameter viele Möglichkeiten in der Steuerung bestehen. Ich denke, bei der aktuellen Generation des Manipulators bietet Jorns nun eine einfachere Steuerungsmöglichkeit an. Ich musste für uns noch einen anderen Ansatz finden“, bestätigt der Experte. „Fest steht: An diesem Projekt haben wir alle sehr viel gelernt und lernen immer noch weiter. Es ist ein langfristiger Prozess, die Anlage dauerhaft in unsere Fertigungsabläufe zu integrieren.“
Automatisierung
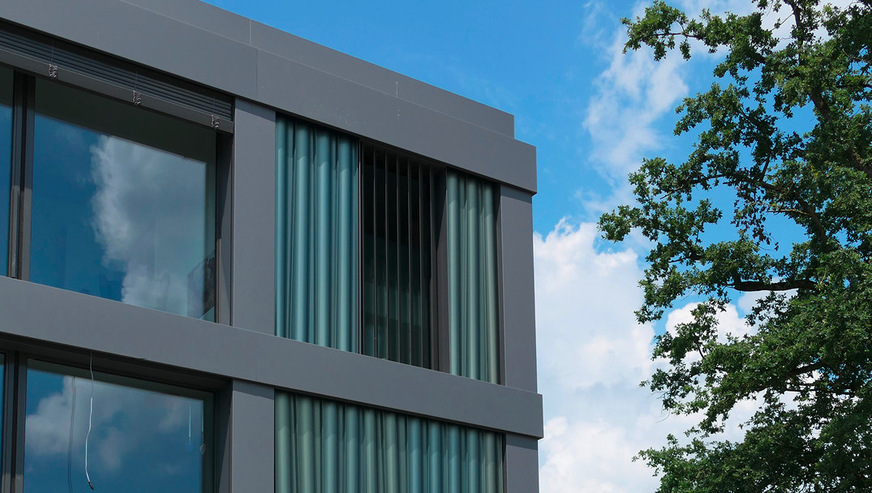
Bild: BAUMETALL
Nach der Übergabe des Zuschnitts an den Doppelbieger erfolgt die vorprogrammierte Biegereihenfolge. Bei Bedarf kann das Blech über die Verfahreinheit gedreht werden. Im Anschluss nimmt die Saugstation die Biegeprofile auf und transportiert diese weiter zur Ausgaberampe. Durch die leichte Schräglage der Ausgabe gleitet das Profil getaktet zur Entnahmestation. Am Ende werden die fertigen Kantteile von der Auflage entnommen und weitertransportiert. Begleitet wird der Prozess vom leisen Surren der emsigen Robotertransporteinheit.
Im Profilmanipulator selbst ist keine Spaltanlage integriert. Die vorgefertigten Zuschnitte werden auf einem Tisch positioniert und anschließend an das während des Betriebs geschlossene System übergeben. Dies kann durch zwei Tore an unterschiedlichen Stellen im Sicherheitssystem erfolgen. So können verschiedene Zuschnitte und Materialien für die Weiterverarbeitung in der Anlage auf Abruf bereitgehalten werden. Das Unternehmen arbeitet mit Großtafelformaten und verfügt außerdem über eine Längs- und Querteilanlage. Beim Blick durch die hochmoderne Werkstatt fällt jedoch auf: Es fehlt an Material. Ein großer Schacht auf der anderen Seite der Halle birgt des Rätsels Lösung.
Es geht hinab
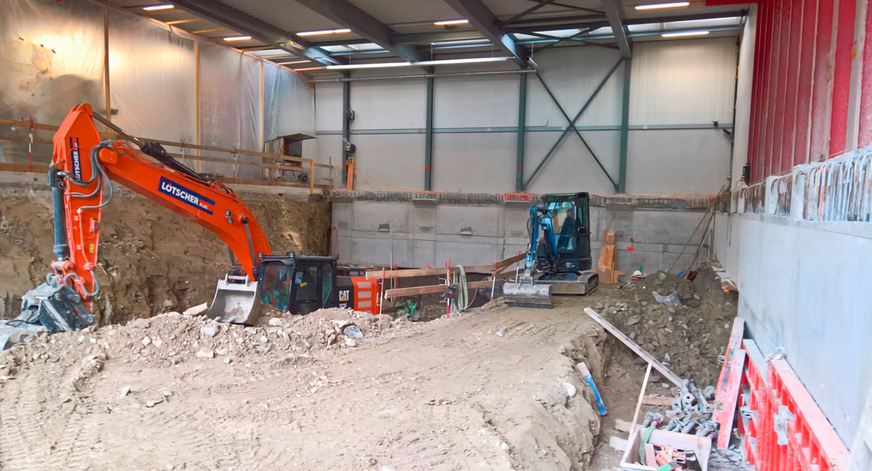
Bild: Josef Wey AG
Mit der letzten Hallenerweiterung im Jahr 2006 war der oberirdische Platz der Wey AG ausgereizt. Größere Auftragsvolumen und die Planung des Profilmanipulators führten dazu, dass ein Platzproblem entstand. Nach einigen Überlegungen kam Josef Wey eine auf den ersten Blick etwas unkonventionelle Idee. „Wir haben uns dazu entschieden, 8 m in die Tiefe zu bauen und unterhalb der Werkstatt unser Materiallager zu errichten.“ Doch nicht nur das. Da aufgrund der Mitarbeiterzahlen keine ausreichenden Parkflächen vorhanden waren, kam auch eine Tiefgarage auf zwei Etagen hinzu.
Um das Projekt zu verwirklichen, wurde im Jahr 2017 bei laufendem Betrieb die Baugrube errichtet. „Das war schon eine etwas verrückte Zeit“, erinnert sich Wey: „Mitten in der Halle war ein großes Loch und in dem stand ein Bagger. Drumherum haben wir weitergearbeitet und in der Baugrube ging es langsam in die Tiefe.“
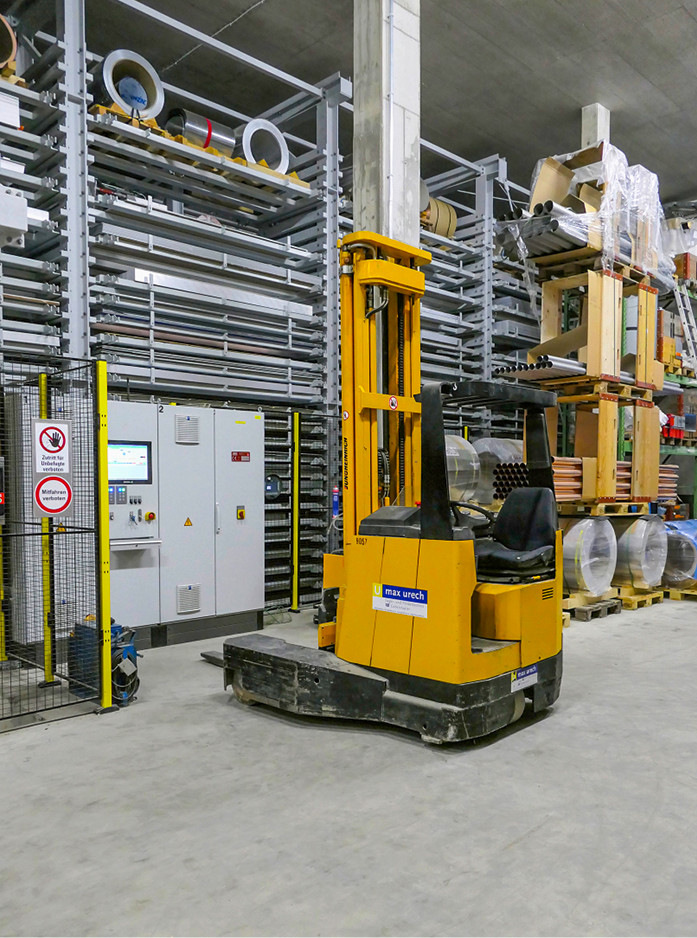
Bild: Josef Wey AG
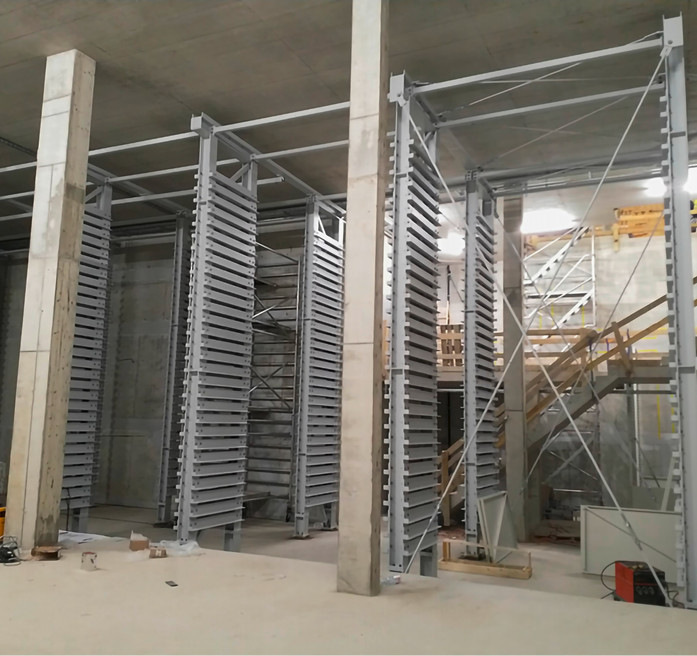
Bild: Josef Wey AG
Wer mit Wey ins Gespräch kommt, stellt schnell fest, dass der Unternehmer sich nicht davor scheut, Herausforderungen anzunehmen und Lösungen zu suchen, die von einem standardisierten Ansatz abweichen. Viele Details wurden während des Baus verändert und an die Bedürfnisse des Betriebs angepasst. „Das ist ein Vorgang, den man zulassen muss“, meint Wey. „Wer ein solches Unterfangen wagt, muss im Prozess flexibel sein“, erklärt der Unternehmer mit einem Schmunzeln. „Das macht den besonderen Reiz solcher Aufgaben aus. Wir probieren immer wieder Neues und wenn wir an die Grenzen stoßen, überlegen wir im Team, wie wir diese überwinden können.“
Hoch hinaus
Das Ergebnis in diesem Grenzfall nennt sich ganz nüchtern: Lagersystem zur automatischen Lagerung und Bereitstellung von Metallpaketen. Dahinter steckt ein für einen Spenglereifachbetrieb vielleicht einmaliges Projekt. Um das Platzproblem zu lösen, erfolgt der Materialtransport durch einen Lastenaufzug zwischen Werkstatt und Keller. Dieser fährt in ein Materiallager mit imposanten Ausmaßen: Das Lagersystem ist 30,3 m lang, 8,6 m breit, 7,1 m hoch. Seine 391 Lagerplätze sind mit einer Nutzlast von je 3000 kg ausgestattet.
Das automatische Beladesystem fährt im Keller-Hochregal an den gewünschten Lagerplatz. Dort übergibt die Verfahreinheit die Palette nach Anwahl auf den Übergabetisch, dieser fördert das Material weiter in den Lift und von dort weiter in die Produktion. Danach kann es entnommen und zur Weiterverarbeitung an die Maschine transportiert werden. Wenn die Palette zurück ins Lager geht, wiegt das System den Restbestand automatisch und ermittelt so den Mengenbestand für die Lagersteuerung. Der Ablauf ist einfach, effizient und gut steuerbar. Dabei sieht Josef Wey Verbesserungspotenzial in seinem System. Für die Zukunft stehen noch einige Möglichkeiten im Raum.
Das unterirdische Lagersystem verlässt der Besucher durch ein Treppenhaus an der schmalen Unternehmenszufahrt und kommt am Ende wieder da an, wo er gestartet ist. Vom verborgenen Riesen ist auch nach dem Besuch von außen nur wenig zu erkennen. Was bleibt, ist der positive Eindruck eines Spenglerfachbetriebs, der den Herausforderungen der Zukunft offen und mit innovativen Ideen begegnet.